Walthers GP9M decoder installation
These series of pictures show how to install a TCS T1 decoder in a HO scale Walthers Trainline GP9M locomotive. This inexpensive locomotive was produced before DCC gained popularity, so the decoder has to be hard wired.
The first step in the process is to remove the weight bar and motor. Be sure to mark the motor to remind yourself which terminal is which. There's no distinguishing marks on this motor to indicate which terminal is which.
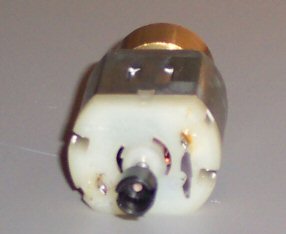
Pic 1 - Marked Motor
Next, since the pick up wires are both black, I used some heat shrink tubing to indicate which ones pick up from the right-hand (respective to the front of the engine) rail. I verified this by placing the locomotive on a piece of track and measuring the resistance with an ohm meter. A reading of close to 0 ohms means the wires connect.
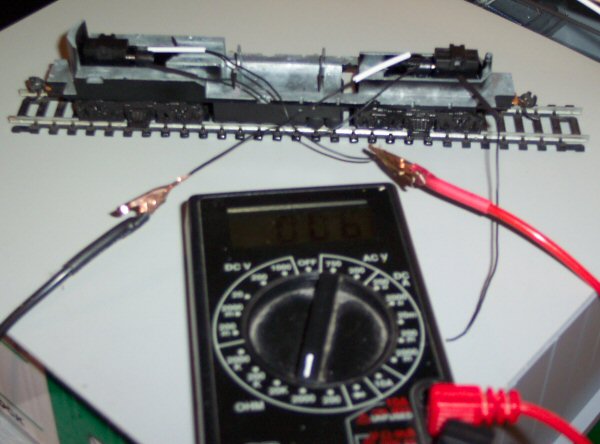
Pic 2 - Pickups and multimeter
I followed the directions as to which wire went where, placing heat shrink tubing on any solder joints. After everything was connected, I then thought about where the decoder would mount. Big mistake. I should have thought of that first, as my initial mounting point would not allow the shell to be replaced on the
locomotive.
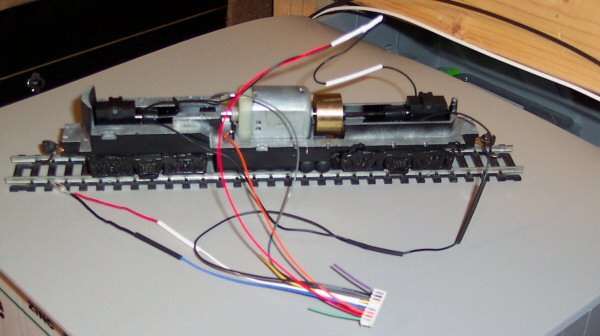
Pic 3 - Connected Wiring

Pic 4 - Initial decoder placement
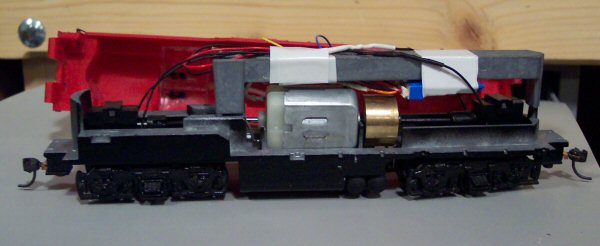
Pic 5 - Finished Installation, before shell is reinstalled
Notes:
1. All wire-to-wire solder joints were made using a "Western Union Splice." Simply overlap the exposed wire at the halfway point and twist the left wire around the right side, and the right wire around the left. This method makes a very smooth joint, allowing
heat shrink tubing to easily seal the joint.
2. Trim your wires, but leave at least an inch extra in case something goes wrong. I had a difficult time with making the motor power connection and wound up having to extend the orange wire.
3. These pictures have been submitted to TCS for use on their webpage. They're welcome to use them if they desire.
This post has been edited at 2008-01-28 19:34:04